Backpack Manufacturer's Complete Production Process: A Transparent Behind-the-Scenes Look
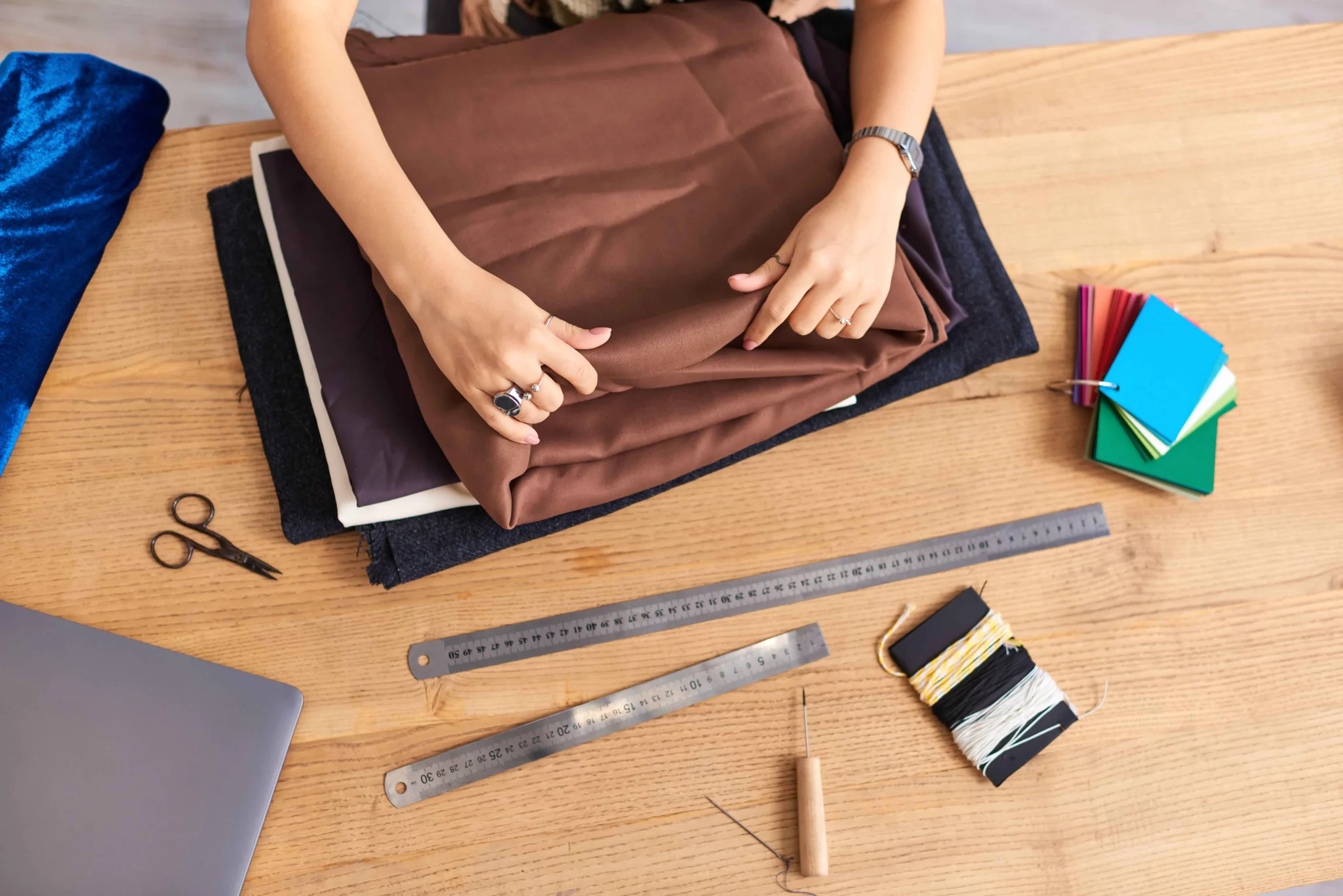
With the increasing demand for high-quality and durable backpacks, understanding the manufacturing process behind these products has become more important than ever.
In this article, we aim to provide a clear and transparent overview of the complete backpack manufacturing process. Whether you’re a brand looking to create custom designs or a business partner exploring collaboration opportunities, understanding the steps involved in production is crucial for a successful partnership.
1. Order Confirmation and Material Procurement
Once your production order is confirmed, the factory begins by organizing the order details, including the quantity and design specifications. The first step is to procure the raw materials. In China, this process typically takes 2-3 weeks, but certain suppliers may require more time. Such as YKK zippers, Duraflex buckles, and Cordura fabrics might take over a month to order.
If you’re working with production facilities in countries like Vietnam, Indonesia, or Cambodia, raw materials are often imported from China or other countries. The additional transportation time should be considered as well. For instance, shipping materials from China to Vietnam can take 2-3 weeks. This means materials that would typically arrive in the factory within 20 days in China might take over 45 days to reach Vietnam, highlighting one of the key reasons why production timelines in China are generally faster than in other countries.
2. Material Inspection and Cutting
When the materials arrive at the factory, they undergo an initial inspection to ensure quality. Once approved, the production team schedules the cutting of materials. Custom logo fabrics are given priority in this phase, and any special logo printing or embroidery processes are also arranged. After the cutting, each major piece is carefully re-inspected. This process typically takes about one week.
3. Pre-Production Processes
Following the cutting stage, the factory prepares the pre-production steps for assembling the finished product. These include gluings, installing zippers, sewing webbings, linings, mesh, and small pockets, among others. This phase is designed to prepare all components for final assembly.
The time required for this stage depends on the complexity of the product. For simpler bags like kids’ backpacks or daily backpacks, this process usually takes 3-5 days. However, for more complex products such as travel bags or duffel bags, it may take up to 10 days, and generally, it will not exceed 14 days.
4. Final Assembly
Once the pre-production steps are complete, the final assembly process begins. This includes key steps as below:
– Bag Joining: The pre-sewn pieces from the pre-production processes (front, back, and side panels) are stitched together to form the basic shape of the bag.
– Edging: The assembled bag is then reinforced using binding tape, which not only strengthens the structure but also hides stitching for a clean, attractive finish.
– Turning the Bag: The partially finished bag is turned inside out for the final inspection and preparation for packaging.
For instance: GFBags can usually produce around 2,000-2,500 completed backpacks per day, depending on the complexity of the design. For more intricate designs like functional travel backpack, production is generally slower, with an output of about 700-1,000 bags per day.
5. Quality Inspection
Once the bags are completed, they are transferred to the Quality Control (QC) department, where each product undergoes 100% inspection to ensure it meets the factory’s strict quality standards. This is an essential step to maintain consistency and ensure that every bag meets the required specifications before shipping.
6. Packaging
After passing quality control, the products are sent to the packaging department, where the bags are packaged according to the client’s specifications. If no specific packaging requirements are provided, we generally use eco-friendly PE bags customized to fit the product size, which are then placed in custom-designed cartons.
We also offer various custom packaging options, including:
– Custom Dust Bags: Available in different materials such as cotton, polyester, or non-woven fabric.
– Eco-Friendly Tape: Various types of tape, including biodegradable and recyclable PE options.
– Inflatable Packaging: For products that require shape retention, we use inflatable bags, which some clients may also request to have their logo printed on.
– Custom Printed Cartons: We can print shipping marks and client logos on the outer cartons for easier identification upon arrival.
Conclusion
The complete production process for backpacks involves several detailed steps, each of which plays an essential role in ensuring the final product meets the highest standards of quality and functionality. By understanding the full scope of the production process, brands and business partners can make more informed decisions when choosing a manufacturer.
If you’re looking for a reliable backpack manufacturer to assist with your production needs, don’t hesitate to get in touch with us. Our team is ready to discuss your project and help turn your vision into a reality.
Post Views: 17